In the demanding environment of a hot plate rolling mill, precise profile measurement of plates is essential to ensure quality standards and operational efficiency. When a customer approached Sapotech with the need for such a system, Sapotech took action to meet the customer’s needs. In response to the customer’s request, Sapotech developed and engineered a tailored solution that met their specific needs.
Typically, in plate mills, similar measurements are performed from below the roller table. However, this method often encounters challenges due to limited space for positioning cameras and illumination equipment. In this particular case, the primary requirement from the customer was to have a system that could perform dimensional measurements from above the roller tables. To address the constraints set by the customer, Sapotech developed an innovative solution capable of performing accurate shape measurements from above the roller table. Notably, Sapotech was the only supplier able to offer a solution capable of performing the required measurements from above the hot plate.
Reveal CAST is typically used as a hot/cold surface inspection system in metals industry, based on systematic measurement and visualization of the target. The system captures image data with high resolution cameras, presenting a real-time picture of the entire target for immediate operator interaction. This visually accessible data is documented and stored for possible post-analysis. By combining modern laser-enabled measurements with super resolution imaging, Reveal CAST can perform precise dimensional measurements. In this case, the measurements were made for very large objects as they pass the Reveal CAST imaging equipment. In Figure 1, the configuration of the system is illustrated, followed by a more detailed description of the setup.
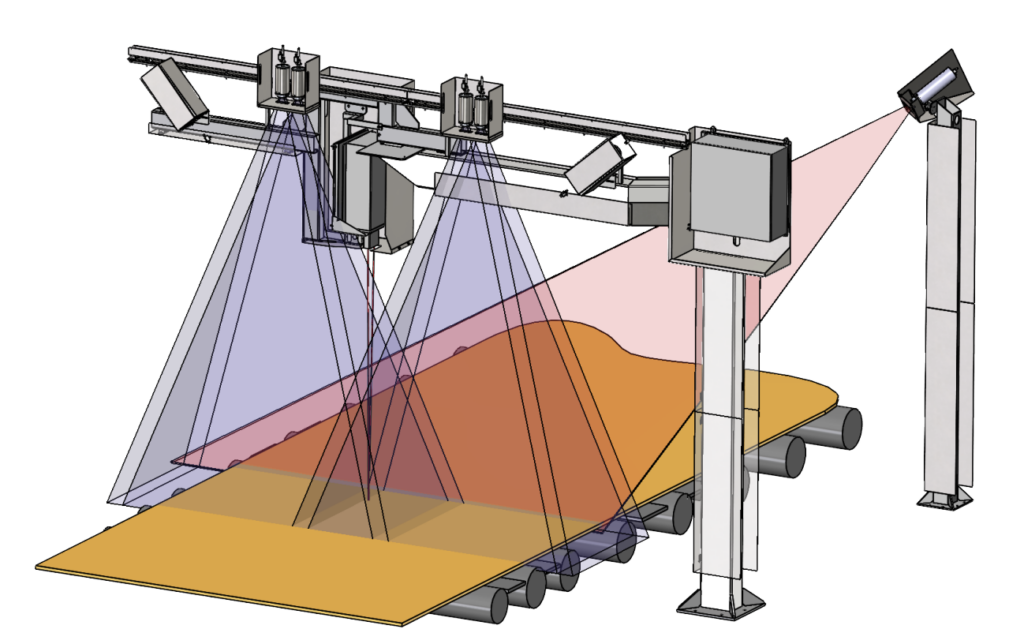
Figure 1. Illustration of the configuration.
Reveal CAST hardware and software is designed to be adaptable, making it suitable for specific customer needs. Therefore, it was possible to use Reveal CAST in this application for width, length and perimeter measurements, i.e. as a plate outer dimension gauge. In width measurement, the plate’s surface (ranging from 900 to 3600 mm) is illuminated to identify its edges. The illumination is installed above the plate line, illuminating the surface after the hot straightening machine. High resolution cameras in the same area capture images from the top side of the plate, detecting the plate edges, head and tail. In addition, it was crucial to install the Reveal CAST equipment at least one meter above the roller track, as plates coming from the straightening machine could potentially collide with it. Figure 2 presents the reference picture of the user interface.
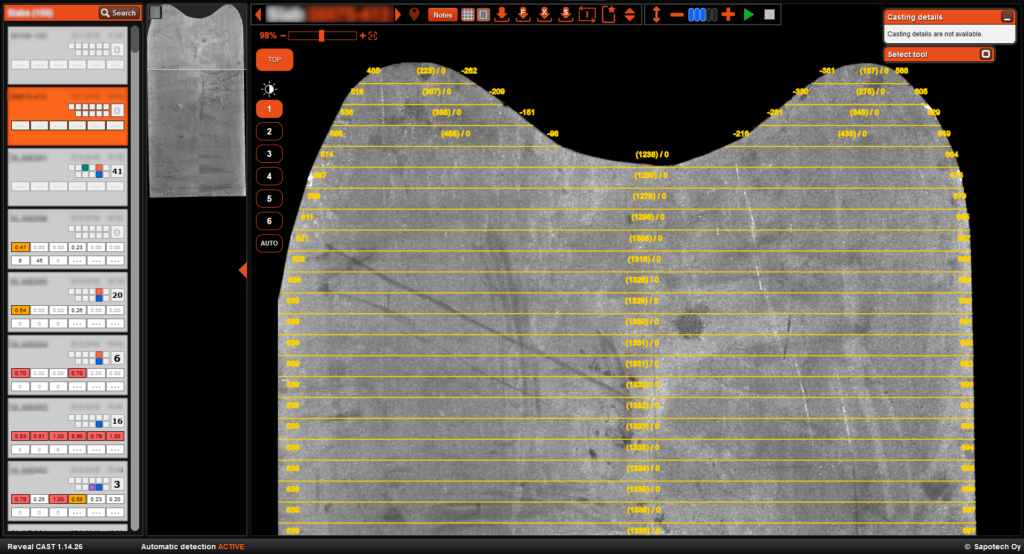
Figure 2. Reference picture of the user interface.
Additionally, a line laser and dedicated cameras enabling 3D profiling are installed to compensate the waviness (edge raising) of the plate in width measurement from the images. This way, the measurement error caused by camera perspective distortion and plate waviness can be eliminated. An additional laser doppler is used to measure the plate’s length. By combining data from these sensors, the length coordinates and corresponding edge locations are calculated. The plate width can be measured with an accuracy of 2 mm at the measuring point. The line laser results help determine edge locations when the plate edges are not in a planar position (as the line bends if the plate is not flat). Figure 3 presents the measurement results of a plate.

Figure 3. Measurement results in the user interface.
According to the customer, Sapotech showed determination and problem-solving skills throughout the project, addressing challenges as they arose. The customer also highlighted that communication with Sapotech was effective and contributed significantly to the project’s success.
Sapotech’s innovative approach to plate outer dimension gauge using the Reveal CAST system has provided a significant advancement in environments with limited space. By offering versatile and accurate solutions tailored to specific customer needs, Sapotech ensures precise width, length and profile measurements from above the process line. This advancement not only enhances operational efficiency but also maintains high quality standards in plate production.
If you have any questions or need a tailored solution for your specific measurement needs, please do not hesitate to contact us. Our team at Sapotech is ready to assist you with innovative technologies and expertise to help you to achieve your operational goals.